Research
- Home >
- Technologies >
-
Design of hygienic blood collection system for poultry slaughterhouses
RESEARCH
Design of hygienic blood collection system for poultry slaughterhouses
Blood collection methods from poultry slaughterhouses are assessed and designed. Specifically, a hygienic method to collect blood with no solid debris has been investigated. The research involved designing, improving and/or selecting the blood collection troughs, pipelines, valves, blood pumps, storage tank and related equipment. The research also involved flow simulations in AnsysTM Fluent. The existing blood collection system in poultry slaughterhouses was reviewed. The slaughterhouse blood uses, equipment needed, blood preservation methods and related processing were also studied. The changes needed were identified and a proposed system was evaluated for both small and large commercial poultry slaughterhouses. The focus was to collect blood hygienically by retrofitting, adding and/or replacing components. The key component is the trough, so various design configurations were studied. Different angles of inclination and variations to the cross-section of the trough were modeled and analyzed using Flow Simulation module in SolidWorksTM. The sensitivity of blood flow rates with respect to angle of inclination was 2.374 ms-1/s/degree. Among a semi-circular, semi-elliptical, trapezoidal, and rectangular cross-section, the most effective for maximizing blood flow volume and velocity was a trapezoidal cross-section. An innovation to the collection system was attaching the trough to a reservoir with a mesh/filter to separate any solid debris like feathers and blood clots from the blood. Also, new materials for piping, blood pumps, valves and other attachments were recommended. AnsysTM Fluent was used for flow analysis to determine the time taken for the mesh/filter to collect debris to determine the mean time between cleaning the screen. For a large-scale slaughterhouse, the blood collection system required cleaning every 6 hours; for a medium-scale slaughterhouse, every 12 hours. This will allow for future automation and/or scheduling workers to complete the task. AnsysTM Fluent also was used simulate the flow of varying amounts of debris within the blood and the time taken for the debris to travel the length of the trough. The distribution of the debris was tracked. As the weight of debris increases, the time taken to cross the length of the trough decreased. The simulations also showed that as the size of the debris increases, the outlet volume fraction of the blood decreased. Hence, the blood flow is impeded when the debris volume and size were large. The proposed system has a 3° angle of inclination for the trough compared to 1° which is typical in existing systems. This increases the blood flow velocity and volume fraction of the debris, as validated using AnsysTM simulations. The highest blood flow velocity and outlet volume fraction was achieved with a trapezoidal cross-sectional trough. For a semi-elliptical trough, the ratio of width to depth (W/D) at ~3 had the maximum blood flow rate. Both troughs had the same top width of 1.2m and similar depths of 0.35 to 0.4 m. The simulations also showed that the blood flow decreases when the viscosity and density of the blood increases; the sensitivity was -0.51667 kg-s/m2 based on changes in blood viscosity. The future work could include constructing a pilot plant of the proposed system to evaluate and optimize the blood collection processing further to promote hygienic blood collection from the slaughterhouses.
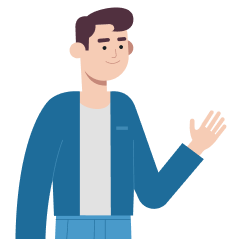
To view more project details and submit an expression of interest
Explore more projects
Solutions to Business Technological Challenges
-
RESEARCH
28 Jun 2023
Peter BarrVancouver
- Nano-structured binding systems
- Environmentally friendly refractories
- Low-temperature fired magnesia bricks
- Non-ferrous smelting refractories
-
-